Recently, the HyDeploy team were thrilled to have such a strong attendance at our webinar, with around 200 people logging in and a stream of engaging questions.
In fact, we received so many that we’ve had to produce this blog and the next one to try to meet demand. There is such huge interest in this project and we believe in it so firmly that we’re happy to provide some answers here.
This week we thought we would start with some great technical ‘myth buster’ type questions about hydrogen as well as one about the wider landscape.
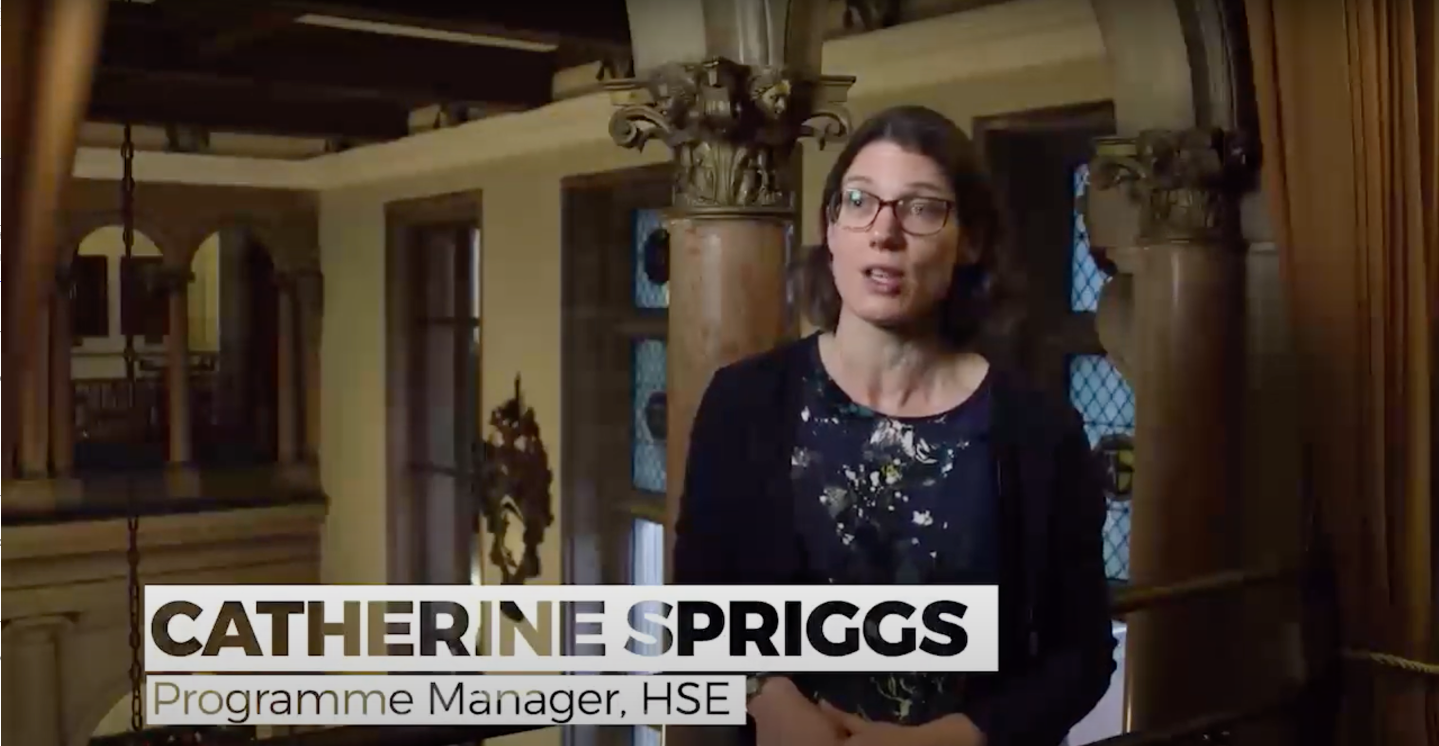
What research has been undertaken with regards to NG/H2 blend stratification/separation in ‘dead leg’ situations or downstream pipework that is not used for a period of time. For example, during plant shutdowns. Would this lead to H2 becoming separated in vertical lines for example?
This is a question we have been asked many times, and is clearly an important issue to understand, so we had to address it in our safety case. We did this in a couple of ways. We undertook some detailed theoretical analysis of our own, but we also used some useful experimental data from a project being undertaken on blending gas in France (the GrHyd project).
Our analysis showed that if we had an absolutely perfectly stagnant pipe with no thermal effects or any kind of movement whatsoever over a sufficiently long time, you would need a vertical dead-leg pipe over 100m tall to achieve a 0.1 %volume change in hydrogen concentration up the pipe, so if we had 20% volume hydrogen at the bottom it could be 20.1% at the top. That difference would be extremely hard to measure. The GrHyd project had also undertaken some practical tests which concluded that there would be no separation observed in reality, even for a height of 1 kilometre. That is three times the height of the Eiffel tower!
Fundamentally the concept of entropy tells us that creating order from chaos requires effort. If we had found it was that easy to separate bulk quantities of hydrogen from methane, we would be making our fortune in the gas processing industry…
What considerations, if any, have been given to the porosity of the network? The hydrogen molecule is notably smaller than the methane molecule, so surely has a chance of being “lost” from the gas blend.
Again, this was an important question to address in our safety case. Managing leakage on the network is an important part of the day to day job of the Gas Distribution Networks, as well as their longer-term asset replacement programmes, to keep us all safe.
Now, it is true that hydrogen is a smaller molecule than methane, with a kinetic diameter of around 280 picometres (that is 280 billionths of a millimetre!) compared with 380 picometres for methane. The actual diameters are even smaller than this. At a microstructural level, in some materials, it is, therefore, true that hydrogen can migrate faster than methane. However, actual detectable leaks on a network or installation typically happen through hairline cracks at joints or damaged pipes. You would typically need a non-destructive measurement technique to detect these kinds of cracks – which would be maybe 100-500 micrometres (that is a tenth to a half a millimetre). These microscopic cracks are therefore around a million times bigger than both methane and hydrogen.
Imagine two vehicles coming up to a checkpoint – one is a car (hydrogen) and one is a lorry (methane). If the width of the checkpoint represented that hairline crack relative to the size of the vehicles it would be around 25 thousand kilometres wide, or twice the diameter of the Earth! As you can imagine across that width, the checkpoint has no chance of ‘sieving out’ the cars from the lorries, or the hydrogen from the methane! This also gives a good picture of the relative leak rate at a molecular level compared with what actually happens through a physical crack.
Just as for the last question, if we had achieved this separation so easily, we would be making our fortune in the gas processing industry.
Are current boilers compatible with working with blended gas? Was there any modification of the distribution network, eg lining of pipe etc.?
These two questions go to the heart of the HyDeploy project. The project purpose was to establish a level of blending into the gas network that would not require any changes to our boilers and appliances in our homes, nor changes to the gas network itself. That way, it enables us all to reduce the carbon we emit from our heating without disruption or installing new equipment. Even at 20% volume hydrogen in our gas network, that is the equivalent carbon saving of taking 2.5 million cars off the road. It also helps us get used to hydrogen becoming part of our energy mix, builds up the supply of hydrogen and associated infrastructure such as carbon capture and storage, as well as developing the supply chain.
To demonstrate that no changes were needed, as part of our safety case, we undertook extensive appliance testing. We did this in specialist test laboratories (KIWA in Cheltenham and the HSE Health and Safety Research Centre in Buxton), but also in homes on the Keele campus where we connected gas bottles with the blend to customer appliances to make sure what we observed in the field reflected what we had seen in the lab. The independent Gas Safe engineers who undertook the field testing reported that all appliances and pipework at Keele that were found to be safe and tight, respectively, on natural gas were also safe and tight with a blend – with no exceptions. Now that we are in the demonstration phase we are also putting eight instrumented boilers through their paces as further confirmation, for the boiler manufacturers to strip down afterwards and assess. Similarly, with regard to the network, we undertook extensive materials testing to show that the pipework would remain safe for the duration of the trial with the blend, and also have some material samples in the live network for testing again afterwards.
Hydrogen is crucial to the UK’s ambition to net zero, what are the real barriers from the team’s perspective?
This is a big question that we will come back to in subsequent responses, as there are a number of important aspects to address. This time let’s pick up the biggest enabler we need – an appropriate policy framework.
Until we fully internalise the costs of the damage that emitting carbon is doing to our environment, low carbon solutions will typically be more costly than business as usual. Therefore, an appropriate policy framework is required – such as what we have for offshore wind and solar. This has been very successful in enabling growth whilst driving down costs with scale and competition. We need the same kind of approach to enable hydrogen to play its part. Government is working to develop this for hydrogen, and has recently set up a Hydrogen Expert Group with industry. However, there is a real urgency required.
As we seek to rebuild and energise our economy following Covid-19, there is an increasing recognition that low carbon infrastructure has a key role to play. Both the Committee on Climate Change and the National Infrastructure Commission see hydrogen as integral to this in their recent letters to the Prime Minister and Chancellor respectively. To make that happen requires urgent, focused and joined-up policy regimes to enable ‘shovels in the ground’. The technical and regulatory success of the HyDeploy project needs to go hand in hand with frameworks to enable investment to see actual projects delivered.